Study Notes
Operations: Methods of Production (Overview)
- Level:
- AS, A-Level
- Board:
- IB
Last updated 22 Mar 2021
The various methods of production are not associated with a particular volume of production. Similarly, several methods may be used at different stages of the overall production process.
Job Method
With Job production, the complete task is handled by a single worker or group of workers. Jobs can be small-scale/low technology as well as complex/high technology.
Low technology jobs: here the organisation of production is extremely simply, with the required skills and equipment easily obtainable. This method enables customer's specific requirements to be included, often as the job progresses. Examples include: hairdressers; tailoring
High technology jobs: high technology jobs involve much greater complexity - and therefore present greater management challenge. The important ingredient in high-technology job production isproject management, or project control. The essential features of good project control for a job are:
- Clear definitions of objectives - how should the job progress (milestones, dates, stages)
- Decision-making process - how are decisions taking about the needs of each process in the job, labour and other resources
Examples of high technology / complex jobs: film production; large construction projects (e.g. the Millennium Dome)
Batch Method
As businesses grow and production volumes increase, it is not unusual to see the production process organised so that "Batch methods" can be used.
Batch methods require that the work for any task is divided into parts or operations. Each operation is completed through the whole batch before the next operation is performed. By using the batch method, it is possible to achieve specialisation of labour. Capital expenditure can also be kept lower although careful planning is required to ensure that production equipment is not idle. The main aims of the batch method are, therefore, to:
- Concentrate skills (specialisation)
- Achieve high equipment utilisation
This technique is probably the most commonly used method for organising manufacture. A good example is the production of electronic instruments.
Batch methods are not without their problems. There is a high probability of poor work flow, particularly if the batches are not of the optimal size or if there is a significant difference in productivity by each operation in the process. Batch methods often result in the build up of significant "work in progress" or stocks (i.e. completed batches waiting for their turn to be worked on in the next operation).
Flow Methods
Flow methods are similar to batch methods - except that the problem of rest/idle production/batch queuing is eliminated.
Flow has been defined as a "method of production organisation where the task is worked on continuously or where the processing of material is continuous and progressive,"
The aims of flow methods are:
- Improved work & material flow
- Reduced need for labour skills
- Added value / completed work faster
Flow methods mean that as work on a task at a particular stage is complete, it must be passed directly to the next stage for processing without waiting for the remaining tasks in the "batch". When it arrives at the next stage, work must start immediately on the next process. In order for the flow to be smooth, the times that each task requires on each stage must be of equal length and there should be no movement off the flow production line. In theory, therefore, any fault or error at a particular stage
In order that flow methods can work well, several requirements must be met:
(1) There must be substantially constant demand
If demand is unpredictable or irregular, then the flow production line can lead to a substantial build up of stocks and possibility storage difficulties. Many businesses using flow methods get round this problem by "building for stock" - i.e. keeping the flow line working during quiet periods of demand so that output can be produced efficiently.
(2) The product and/or production tasks must be standardised
Flow methods are inflexible - they cannot deal effectively with variations in the product (although some "variety" can be accomplished through applying different finishes, decorations etc at the end of the production line).
(3) Materials used in production must be to specification and delivered on time
Since the flow production line is working continuously, it is not a good idea to use materials that vary in style, form or quality. Similarly, if the required materials are not available, then the whole production line will come to a close - with potentially serious cost consequences.
(4) Each operation in the production flow must be carefully defined - and recorded in detail
(5) The output from each stage of the flow must conform to quality standards
Since the output from each stage moves forward continuously, there is no room for sub-standard output to be "re-worked" (compare this with job or batch production where it is possible to compensate for a lack of quality by doing some extra work on the job or the batch before it is completed).
The achievement of a successful production flow line requires considerable planning, particularly in ensuring that the correct production materials are delivered on time and that operations in the flow are of equal duration.
Common examples where flow methods are used are the manufacture of motor cars, chocolates and televisions.
You might also like
Methods of Production
Topic Videos
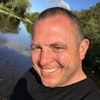
Inside Nissan - Superb Production Video
28th October 2015
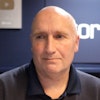
UK Manufacturing - The Kit Kat Supply Chain
6th October 2014
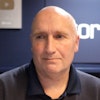
Manufacturing - Inside GSK's Aquafresh Toothpaste Factory
23rd February 2015
Production: Flow Production Method (GCSE)
Study Notes
Production: Batch Production Method (GCSE)
Study Notes
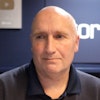
How to Make a Car in 8 Hours (Shown in 60 Seconds)
24th January 2016
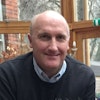
How BMWs are made
17th April 2018