Blog
Q&A - What is involved in quality assurance
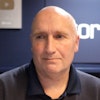
19th December 2009
A definition of quality assurance is: “the processes that ensure production quality meets the requirements of customers”.
This is an approach that aims to achieve quality by organising every process to get the product ‘right first time’ and prevent mistakes ever happening. This is also known as a ‘zero defect’ approach.
In quality assurance, there is more emphasis on ‘self-checking’, rather than checking by inspectors.
Advantages of quality assurance include:
• Costs are reduced because there is less wastage and re-working of faulty products as the product is checked at every stage
• It can help improve worker motivation as workers have more ownership and recognition for their work (see Herzberg)
• It can help break down ‘us and them’ barriers between workers and managers as it eliminates the feeling of being checked up on
• With all staff responsible for quality, this can help the firm gain marketing advantages arising from its consistent level of quality
Total Quality Management (“TQM”)
This is a specific approach to quality assurance that aims to develop a quality culture throughout the firm. In TQM, organisations consist of ‘quality chains’ in which each person or team treats the receiver of their work as if they were an external customer and adopts a target of ‘right first time’ or zero defects.